Munro Live Dissects Tesla’s Cybertruck Front Structure
Sandy Munro’s team performs a virtual teardown of Tesla’s promised pickup’s front subframe.
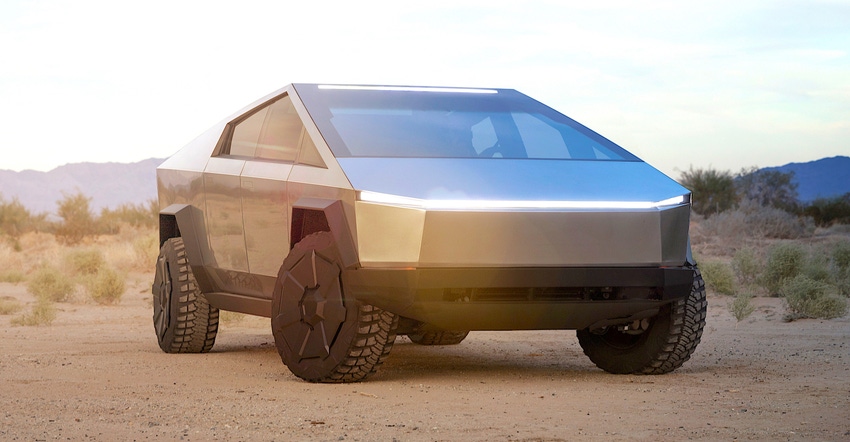
Tesla has not released much detailed information on the planned Cybertruck despite that truck being two years behind its originally announced availability date if it goes into production by the end of 2023.
However, the company did post a short video on Twitter demonstrating the Cybertruck in a crash test lab just prior to impact with the barrier in a full-frontal impact test. The engineering team at Munro & Associates took the opportunity to analyze some of the truck’s front structure which is visible in a snippet of the video that is shot through the window in the floor right in front of the impact barrier to record the movement of chassis parts as the truck absorbs the blow.
Each of the components is color-coded, making post-impact video analysis easier for Tesla’s engineers. This also helped Munro’s engineers, and they posted a video on their Munro Live YouTube channel discussing what they can see. Corey Steuben, president of Munro & Associates tag teams with Munro program manager Jordan Arocha in this analysis.
Jordan Arocha: Based on the geometry, these look like forged lower control arms. The red is the primary subframe or the cradle. This is carrying the suspension, likely a large portion of the drive unit, the gearbox, and so forth, also making primary connections of those control arms inboard to the vehicle structurally.
The yellow [parts] are the primary longitudinal rails. That’s part of the body-in-white structure that’s the primary impact structure at the front end of the vehicle. It is also what this subframe is going to mount to, principally.
At the leading edge here we’ve got these little green pieces. Those are going to be your crush cans. Just looking at them, I’m going to make an assumption that they are likely extruded aluminum.
At the bottom of the subframe, we see this pseudo X-member. You’ll notice a lot of X-member-like geometries in this suspension system. But this piece right here, it is blurry, it’s kind of hard to make out, its painted light blue; it looks like a multi-piece stamped steel weldment, which we’ve seen in the past.
Corey Steuben: This is a really exaggerated X shape, particularly because these mounting locations for the control arms are very far inboard. This is something Rivian did to get a lot of travel. So the further inboard those points are, the longer the arm is, the more travel you can get while maintaining decent geometry for your suspension. For the Model 3 and the Model Y we have a similar shape.
The front bar is very important for SORB. SORB is Small Overlap Rigid Barrier. It is a test where you are engaging 25 percent of the vehicle. The subframe on the Cybertruck is very wide. It is relatively wide on the Model 3 and the Model Y. But the bar that comes across, this is a solid tube, this needs to be very strong. This one is welded in multiple different places.
What we notice [on the Cybertruck] is that this is secured with threaded fasteners. The reason why this is most likely done is because it is a different material. You could have a very high-strength steel here. When you have such dissimilar metals they are very hard to weld together.
Jordan Arocha: This cross-member is super important to SORB. What it is doing in most SORB events is, depending on how far outboard the geometry of the member it is attaching to on these outboard wings, and the dynamics between the barrier and this corner specifically, this member will either go into compression, meaning it will want to crush cross-car as this starts to load up from that barrier or it will go into tension, which will want to sort of bend these wings down and this will want to stretch or go into tension.
A perfect SORB event would be if the longitudinal rails and the position of all these monuments didn’t really deviate. You want ideally those front longitudinal members, meaning these yellow rails, to maintain perfect congruency from one another. That’s going to keep your vehicle rigid in order to get away from the barrier and if the vehicle goes away from the barrier naturally the occupant is going to be safer.
Corey Steuben: Material choice: Steel is oftentimes the best choice when you need a high amount of strength and a decent weight-to-strength ratio.
We have the Rivian subframe, which is astronomically expensive and heavy. It is 25.5 kilograms and they achieve a lot of the same geometrical constraints here but at a high weight and cost penalty. This is made with a lot of extrusions and plate aluminum.
The Model Y and Model 3 cradle is lighter even though they are using a heavier material. So, a stamped steel weldment oftentimes is a good choice for a subframe.
About the Author(s)
You May Also Like