Survival strategies from the trenches
July 6, 1998
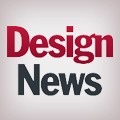
Consider all of the competitive pressures you've ever faced--cost, quality, environmental considerations, and so on. Then multiply the intensity by about ten times. That's how one engineer aptly describes life in the new millennium.
"Expectations have risen so greatly that anything anyone ever considered a competitive advantage is now a given," says Keith Snorek, a mechanical designer at BF Goodrich's Aerospace/Aircraft Sensors Division. "High quality, low cost, quick time-to-market--things like that are just enough to get you in the game today."
David Fadness, a self-employed mechanical engineer who designs medical equipment agrees. "We are definitely in an international market--we're competing with people all over the planet. I live and do business in Silicon Valley, where the prices are just outrageous. For us, cost control is becoming more and more critical."
For engineers at BF Goodrich, the increased pressure means doing everything they were doing before, but doing it better and doing more of it. "We are very fortunate that the reliability and quality of our products have given us a type of leverage in the marketplace that some of our competitors do not have," says Snorek, "But we are constantly challenging ourselves and finding ways to raise the bar."
Dollars and sense. Reducing cost was the challenge cited most frequently (80%) by respondents of Design News' exclusive 1998 career survey. So just how are engineers now planning to cope with this seemingly age-old issue?
"Since it's always better if you can design anything with fewer pieces, we now have a formal program in place to reduce the number of parts in a design, and we've also eliminated a lot of extraneous paperwork in the design process," says Carl Baggett, a structural design engineer for missiles at Boeing.
Also, Baggett continues, Boeing has been able to cut the cost of its missile designs by concentrating on what he says are "the little things that good designers should always pay attention to."
Most assemblies, for example, are now "built up," meaning that an assembler will simply stack each subsequent part on top of the last. "Instead of trying to screw something onto the bottom side of an assembly, we're letting gravity help us," says Baggett.
Manufacturing and engineering go hand-in-hand for Fadness as well. "If you want cost-effective designs, engineering simply cannot work in the absence of input from manufacturing," he says. "You can no longer afford to say, 'Here's the design, you worry about how to build it.'"
Something else Fadness has been doing for awhile now is modularizing his designs where he can. "We've designed a whole group of subassembly modules that we can use across a variety of product lines," says Fadness.
Modularization is also a cost-cutting strategy for John Fitzgerald, a senior mechanical engineer at Phase Metrics, a company that makes test equipment for the disk drive industry.
"By leveraging off of a pre-existing design, we can offer the identical option on two different machines," says Fitzgerald. "We don't have to reinvent the wheel."
Phase Metrics has also found that buying subsystems (versus designing them in-house) can reduce design costs and time-to-market.
"Before, when we needed an x-y motion system, we might buy a bearing, a ball screw, and a motor. We'd take all these separate items and build up that system ourselves," says Fitzgerald. "Today, we'll go to just one vendor and buy the complete system. What we save on is not only engineering effort and time-to-market, but we save in a number of other areas, like receiving and inspection systems and quality control."
Jim Crable, a product design engineer with Rotary Lift, has been able to save money in product redesigns through material substitutions, or sometimes by having components requoted. "In some designs, we've been able to cut costs by going from steel to plastic or other more common materials," says Crable.
Green is good. Another area where engineers are feeling a tighter pinch is environmental regulations, particularly as EPA expands its hit list of toxic materials.
Boeing, for example, went through an extensive effort to eliminate all cadmium-plated fasteners in its designs for the Navy. The cadmium plating helped the fasteners, which are exposed to sea-water, resist corrosion. The alternative was either aluminum-plated or stainless-steel fasteners, both of which were thought to be more expensive.
Standardizing on a fastener design company-wide helped. "The price was pretty much of a wash, because of the volume we were purchasing," says Baggett.
The key factor for Boeing was that it got started early enough on the environmental issue that engineers had sufficient time to find the right solution.
"We kind of stepped up to the plate on this one and voluntarily signed on to meet the guidelines," says Baggett. "We ended up forming a team to look into a whole range of environmental issues to make sure our designs are earth friendly."
Ten top tips for staying alive in the 21st Century
Design News readers share their secrets
1. Modularize your designs whenever possible
2. Exploit the use of computer tools that improve productivity
3. Seek to reduce the number of parts
4. Standardize on components across different designs
5. Seek to reduce or eliminate paperwork
6. Outsource when the alternative is reinventing the wheel
7. Leverage on pre-existing designs where possible
8. Look for opportunities to substitute materials in a redesign effort
9. Bring manufacturing into the design process early
10. Leverage off of your vendors' knowledge of the latest environmental regulations
About the Author(s)
You May Also Like